Technology
The HAMR Process
The Hydrogen Assisted Metallothermic Reduction Process
The HAMR process is our proprietary breakthrough technology developed by world renowned metallurgist, Dr. Zak Fang with funding for the U.S. Department of Energy’s ARPA-E program.
HAMR, which stands for Hydrogen Assisted Metallothermic Reduction, is a patented powder metallurgy process technology that allows for the production of titanium powders. This process can take almost any form of titanium or scrap titanium alloy feedstock and produce titanium powders at very low energy intensity, enabling the potential for low cost, low carbon emission production in a sustainable closed loop. The majority of the energy and emissions savings comes through eliminating the need to chlorinate TiO2 to make TiCl4 and removing the need for vacuum distillation after the reduction of TiCl4.
The HAMR process uses conventional powder metallurgy processing steps to control the size of the particles, add alloying elements, and ensure that the result is high quality titanium powder. Typically, at this stage, titanium powders produced via the conventional Kroll process or other related technologies result in a titanium powder that is high in oxygen content. This is where the HAMR process comes in.
These high-oxygen titanium powders are processed via the HAMR process technology, which reduces oxygen levels below current industry requirements. The process destabilizes Ti-O using hydrogen, making it possible to turn the reduction of TiO2 with Mg from being thermodynamically impossible to thermodynamically favored. This allows TiO2 to be reduced and deoxygenated directly by Mg to form TiH2 with low oxygen levels that can meet the needs of the industry. TiH2 is then further processed to titanium metal through industry standard approaches.
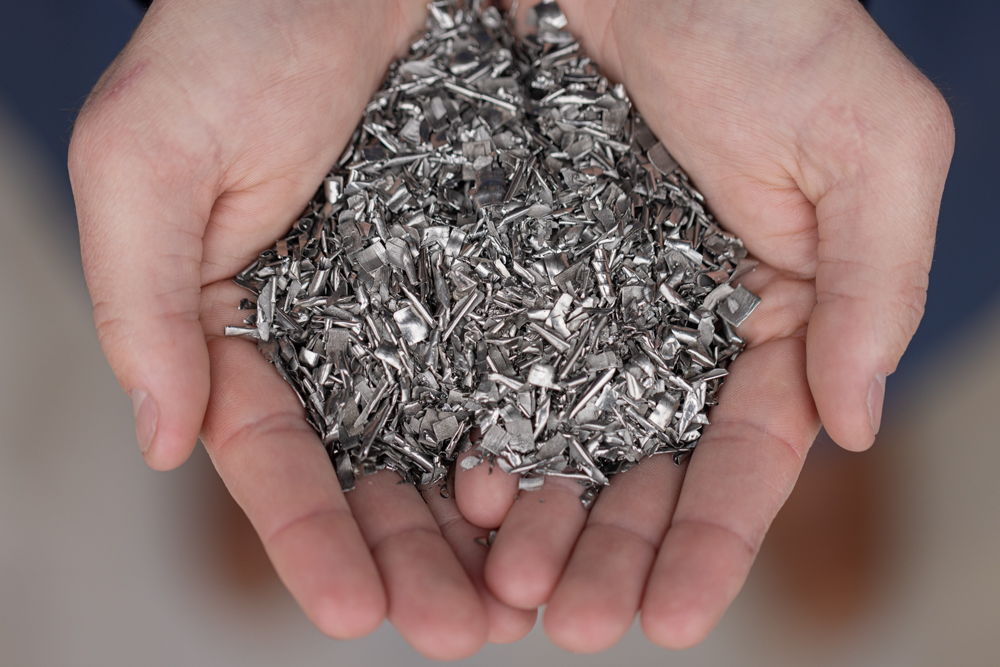
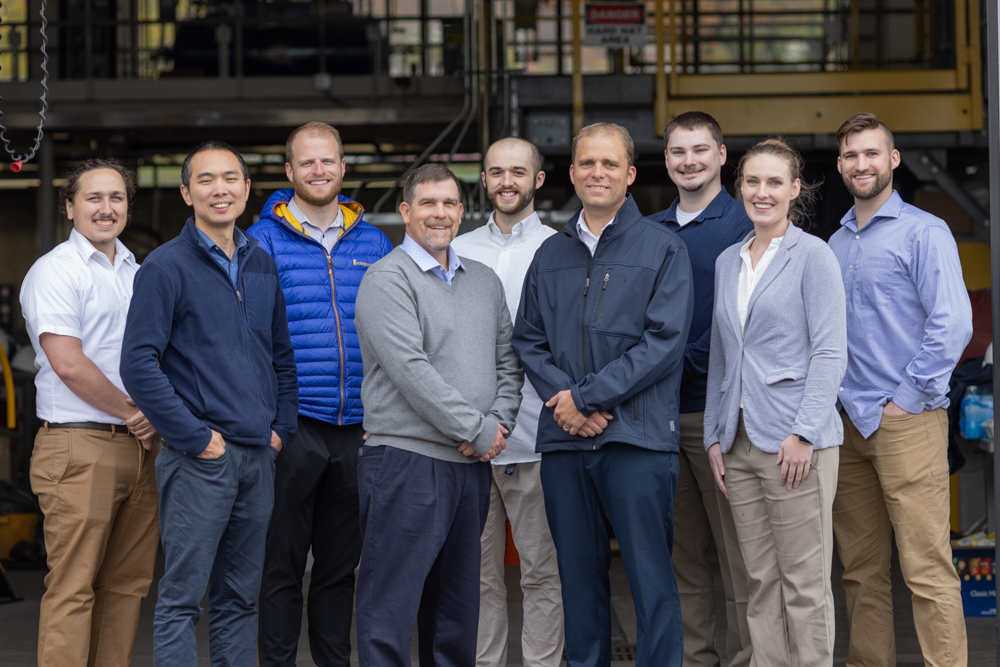
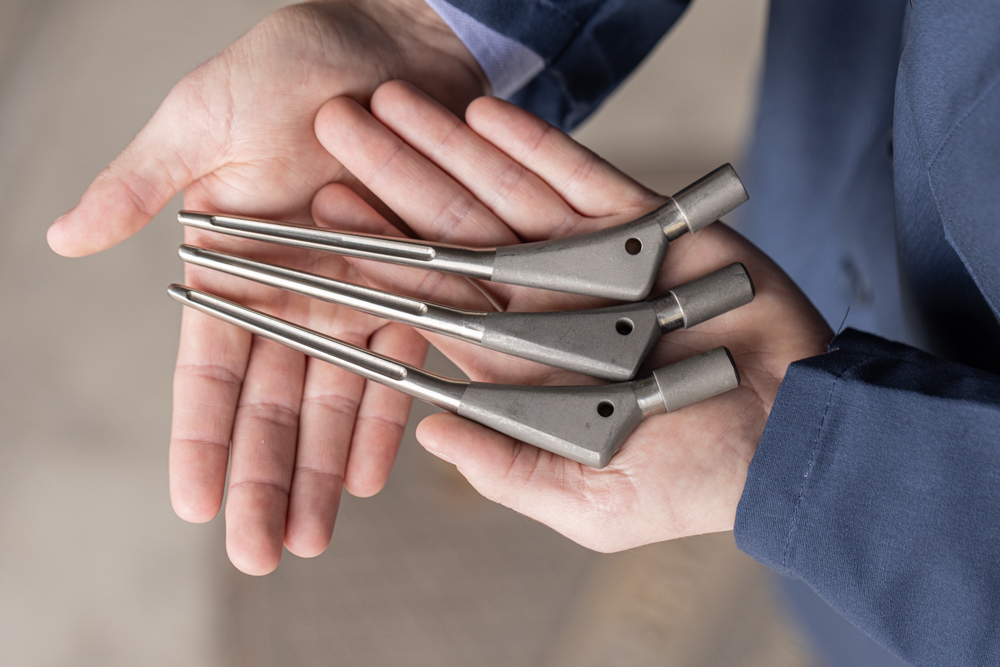
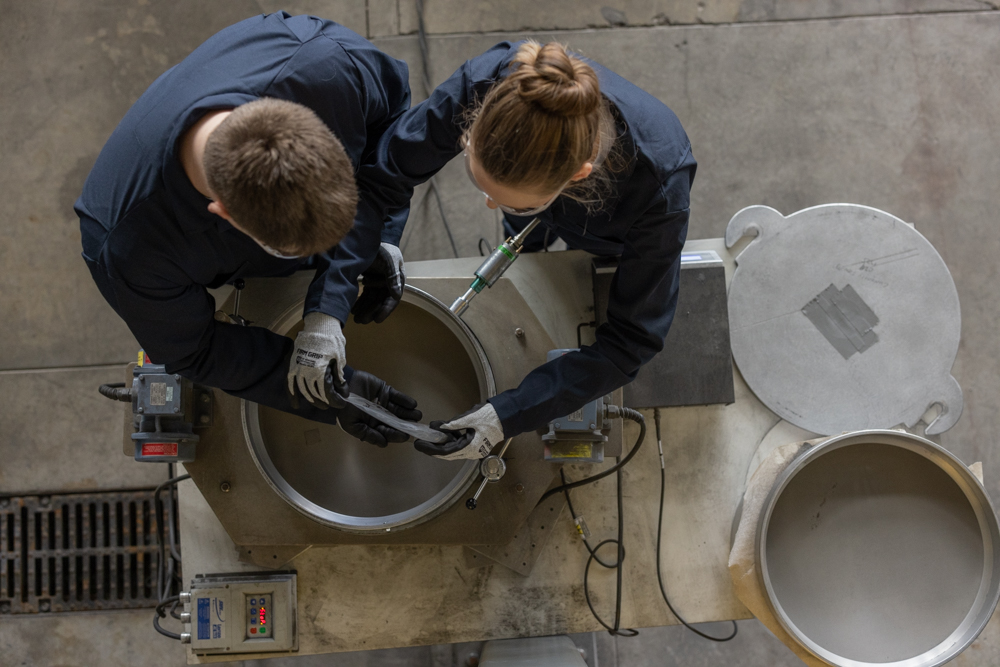