Operations
Metal Operations
Metals
The breakthrough titanium metal technologies offer a potential pathway to a 100% U.S.-sourced, low-cost and low-carbon titanium supply chain that can reduce the carbon emissions of advanced materials. These technologies can accept either raw minerals or 100% scrap metal as feedstock, and are capable producing in a closed-loop, 100% recyclable metal supply chain.
The potential exists to apply these technologies to produce metals other than titanium as well, with research underway into applications for rare earth elements and zirconium.
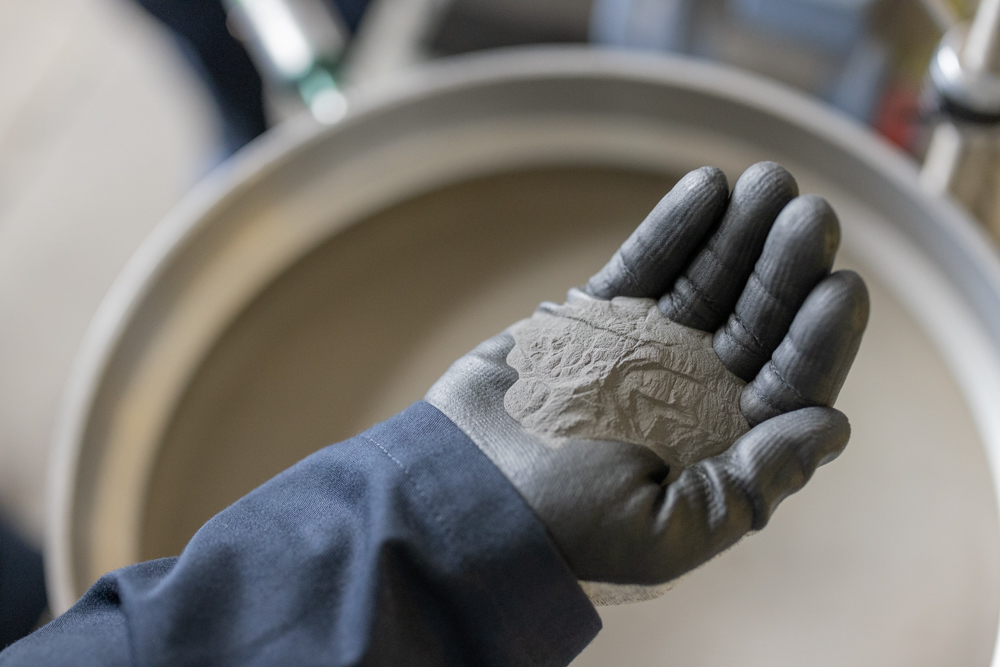
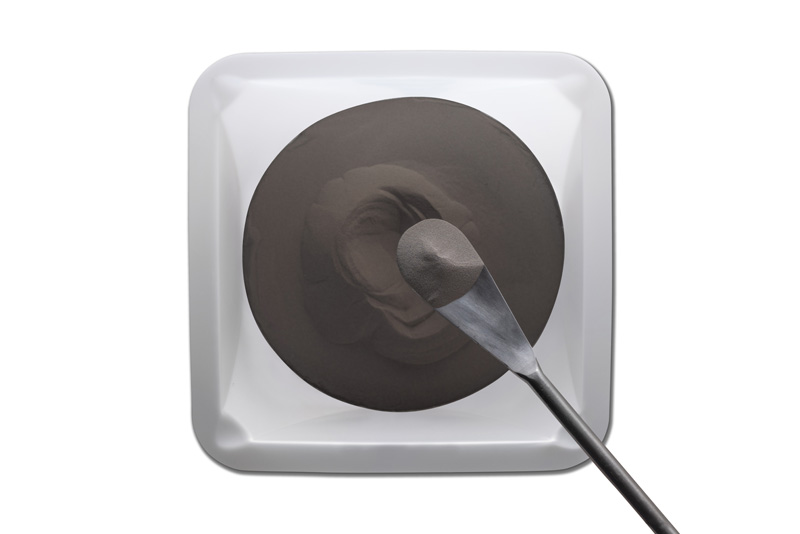
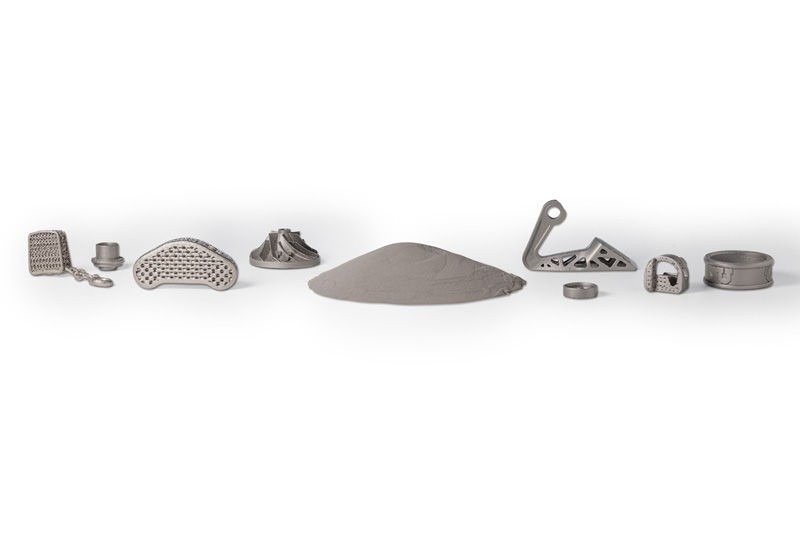
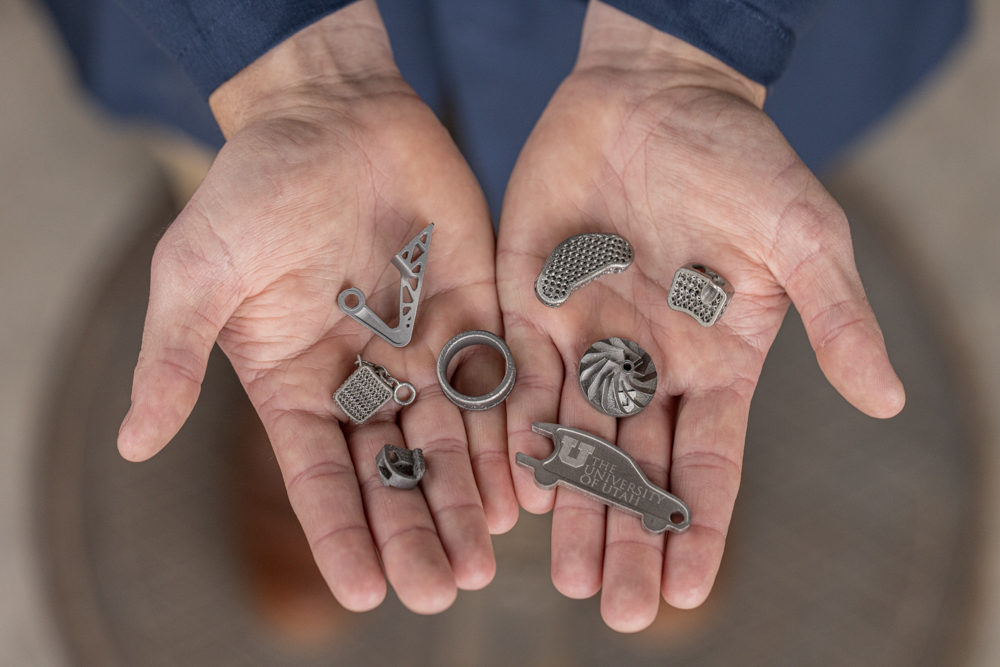
Leading the Titanium Age
Our mission is powered by proprietary technologies invented at the University of Utah and developed with funding from the United States Department of Energy’s (DOE) Advanced Research Programs Agency – Energy (ARPA-E) program.
These technologies enable us to produce low-cost titanium metal from either titanium minerals or scrap titanium metal. The ability to use 100% titanium scrap as feedstock, which is not possible with the industry standard Kroll manufacturing process, allows for a novel, closed-loop and sustainable titanium manufacturing process.
Our Technologies
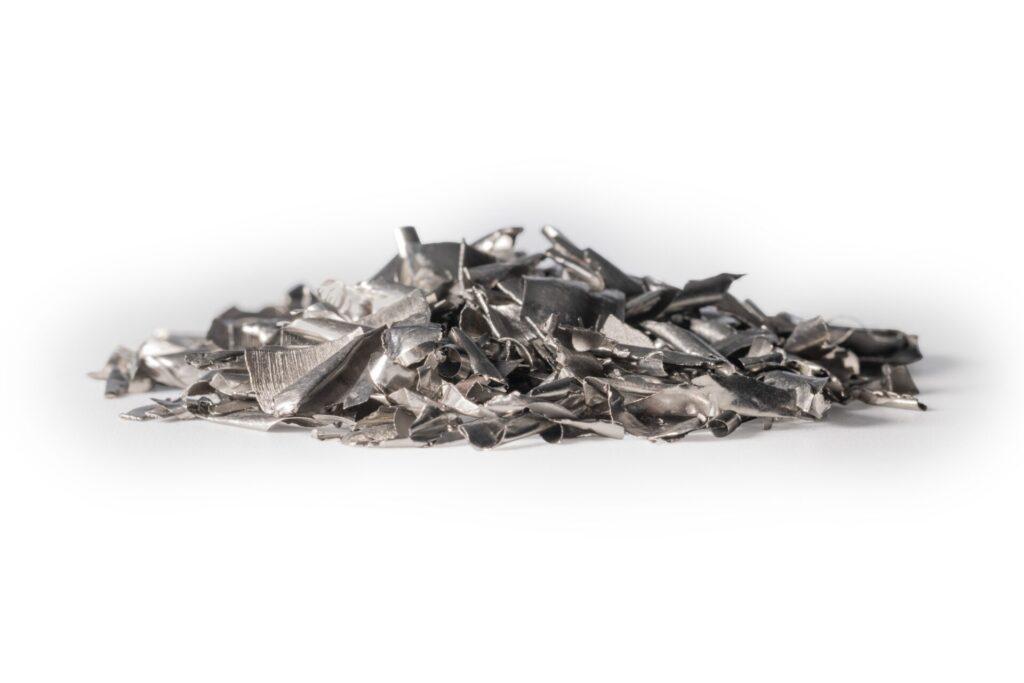
The HAMR Process
The Hydrogen Assisted Metallothermic Reduction (HAMR) process is an energy efficient thermochemical process that can produce either Commercially Pure (CP) or alloyed titanium powders at low cost and with low emissions.
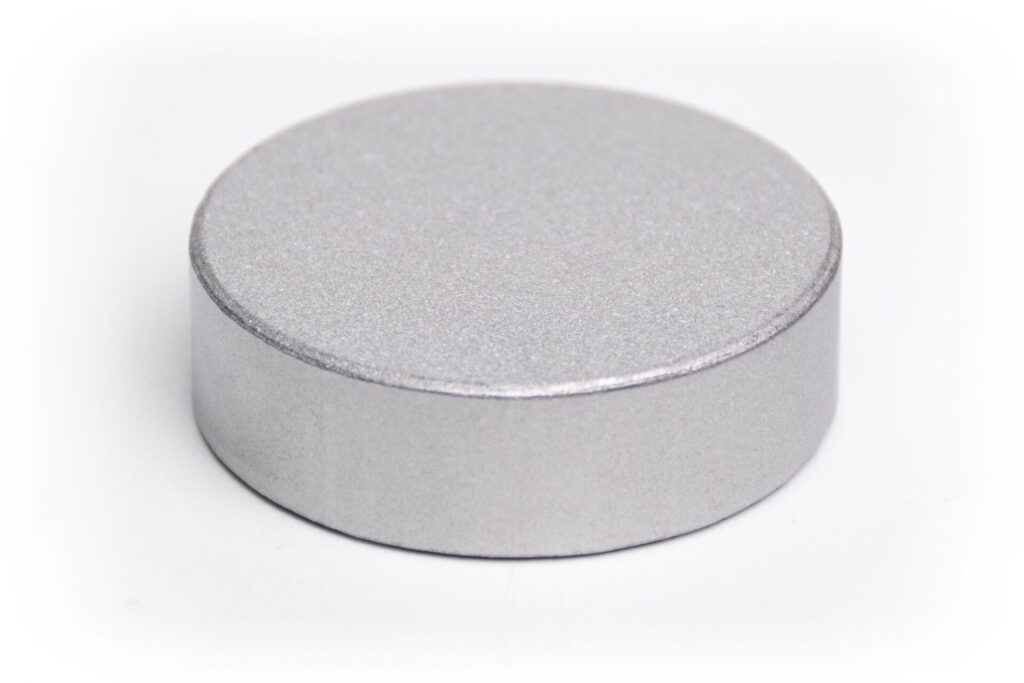
The HSPT Process
The Hydrogen Sintering and Phase Transformation (HSPT) process is an innovative powder metallurgy process that enables the low-cost production of near-net-shape titanium parts with similar properties to traditional forged or wrought parts.
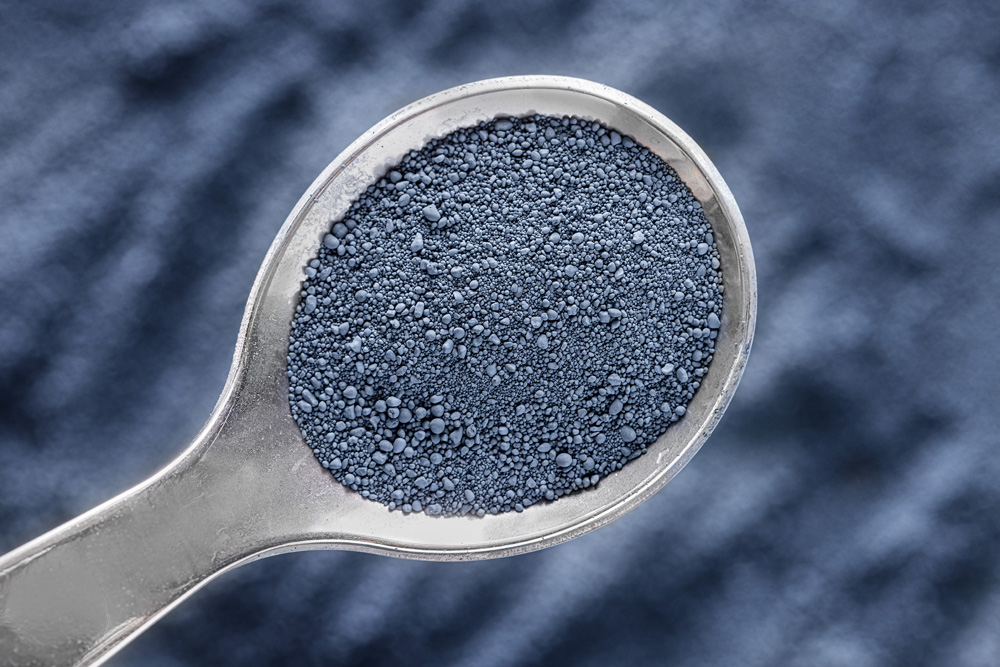
Synthetic Rutile
Process
(Green RutileTM)
IperionX’s Green Rutile is produced via an innovative low carbon titanium mineral enrichment technology that upgrades lower content titanium dioxide ilmenite minerals into a high titanium synthetic rutile product without the use of carbon reductants, including coal, which are typically used to upgrade low grade titanium feedstocks into high value, high grade titanium feedstocks.